Behind the scenes at Focal, France (part 2)
We've been in France to visit speaker manufacturer Focal, and as you can read in our first blog, the company makes its high-end models in its factory in Bourbon Lancy.
During the second part of our visit, we went to the firm's drive unit factory based in St Etienne (below).
Focal is rare among its rivals in that it builds all its home audio drive units in-house. It’s also unusual in optimising each drive unit for the speaker it’s going in, rather than using the same unit across a range, as most speaker manufacturers tend to do.
In-house production gives it the capability to do so. In theory at least, this should give it a strong performance advantage.
Bearing in mind Focal’s obsession with drive unit technology, it comes as no surprise to learn the company started off as a drive unit manufacturer, only building complete speakers later.
The factory doubles as home to the R&D department too, as well as the company’s in-car division and Pro-audio operation.
We had the chance to see the company’s new listening room, which is massive enough to take a pair of Grand Utopias – worth £130,000, around 6ft high and weighing in at 260kg.
Get the What Hi-Fi? Newsletter
The latest hi-fi, home cinema and tech news, reviews, buying advice and deals, direct to your inbox.
We were particularly taken with the wave-like ceiling shape and wooden strips décor used throughout. The room was only completed just before our visit and it’s clear some acoustic fine-tuning is needed. Still, compared to most manufacturers' listening facilities we’ve visited, the new room is deeply impressive.
The rest of the building is given over to drive unit production, with Focal making a staggering 30,000 units a week.
We had a look at the manufacture of the larger drive units first. Focal has a number of production lines. One is automated for high volume units that don’t change very much in specification. The other is for smaller batches, which are made in a much more hands-on way.
While Focal is happy to use a variety of cone materials including polyglass and Kevlar, all its upmarket speakers use what the company calls a ‘w’ cone. Here two tissue-like skins of woven glass sandwich a foam core. The resultant cone is stiff, light and well damped – an ideal combination for any drive unit cone. The engineers are able to fine-tune the mix for each application.
Here's a chart on the factory floor that shows the three basic cone structures with graphs displaying their frequency behaviour:
The speaker manufacturing process
The ‘w’ cone is made using a mould. The tissue sheets of woven glass and foam are placed on the mould and stretched to avoid creases.
Composite tissue put on to mould (above); cones in complete mould ready for treatment (below)
Once the top of the mould is in place, the whole assembly is put under pressure and heated in a special press to form the cone. This process is done in batches. The number of cones that can be made in each batch is dependant on their size.
Moulds in press
The fully formed cones are then put into a laser cutter that carves the cone into shape accurately. It’s vital this is done with precision otherwise the final speaker unit just wouldn’t work properly. Doing the cutting by hand just isn’t possible if a high standard of consistency is needed.
Before and after comparison of cones
Not only is the cone’s the outer edge cut, but the inner hole too, onto which the voice coil assembly is glued. Once the surround and voice coil assembly are glued into a place a special machine is used to secure the spider. The spider, together with the surround, ensures the cone travels in a straight line and doesn’t go too far in either its forward or backward travel.
Attaching the spider
An adjacent line showed the basket (the frame the cone sits in) and the motor structure being made. The chassis and cone are then glued together and tested to make sure the speaker unit’s output is within specification.
Speaker chassis without cone
Tweeters are made up on the first floor of the factory. The company has specialised in inverted-dome tweeters for years, and now uses an aluminium/magnesium diaphragm for most of its products, leaving a highly exotic beryllium dome for its higher–end Electra and Utopia ranges.
Beryllium is toxic in its natural state, so Focal has had to devise a careful manufacturing process to create the domes. Here’s the room where the domes are formed.
Beryllium room (above); beryllium dome (below)
The completed drive units are then mounted into the speaker cabinets together with the crossovers. Chorus 826V floorstanders were being completed during our visit.
Focal’s in-house manufacturing capability is impressive, as is its innovative technology. We’re due to review the company’s £7000 Beryllium-dome equipped Utopia Diablo soon. We can’t wait.
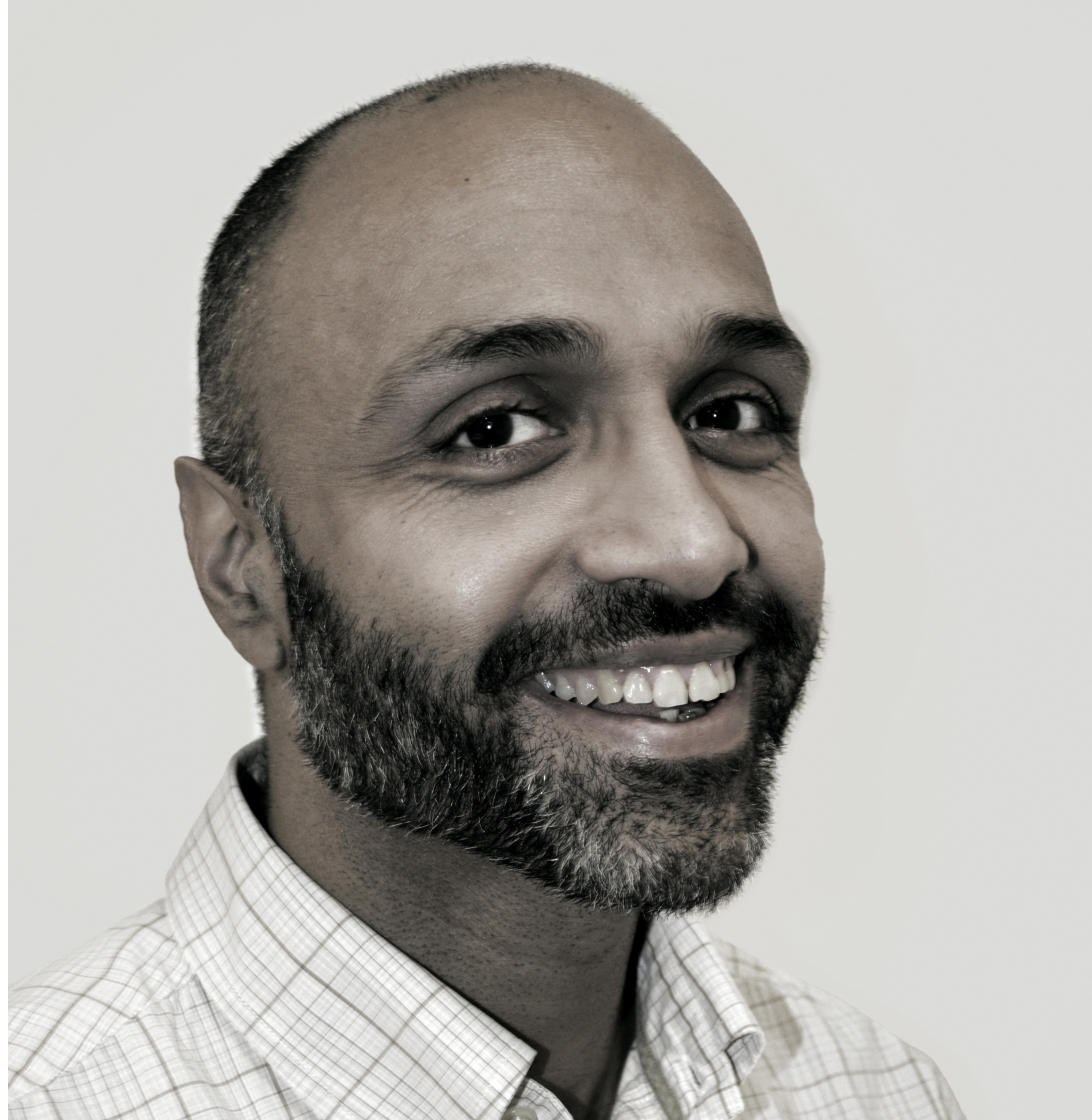
Ketan Bharadia is the Technical Editor of What Hi-Fi? He has been reviewing hi-fi, TV and home cinema equipment for almost three decades and has covered thousands of products over that time. Ketan works across the What Hi-Fi? brand including the website and magazine. His background is based in electronic and mechanical engineering.