Behind the scenes at Focal, France (part 1)
Focal is France’s largest speaker manufacturer with a turnover of around €40m and just short of half the French domestic market. Like other companies of its size, Focal is expanding into new markets such as desktop speakers and headphones too.
Last week we popped over the Channel to take a look around the company’s in-house speaker cabinet factory based in Bourbon Lancy – a small town pretty much smack bang in the middle of France.
It’s not much to look at from the outside, but this unassuming factory (above) is responsible for producing all of Focal’s high-end Electra and Utopia cabinets.
To give an idea of the market sector Focal competes in, the entry-level Electra standmounter, the 1008 Be, costs £3000 while the Utopia range tops out at £130,000. But these are not high-end, one-off 'specials'. In total the Bourbon Lancy factory produces around 25 pieces of Electra, plus around another five pieces of Utopia, every day.
As for the rest of the range, cabinets for the company’s entry-level Chorus range are made in other European factories based in Poland and Italy.
The Production Process
But back to the factory in France. The production process all starts with the necessary raw materials. The company brings in stacks of cut MDF pieces – large uncut sheets would be too cumbersome to store and transport. Here’s the stock of cut boards ready for use:
Get the What Hi-Fi? Newsletter
The latest hi-fi, home cinema and tech news, reviews, buying advice and deals, direct to your inbox.
Most of the speakers require extra thick sections for their front panels. These are made up using differing thicknesses of MDF stuck together. Not only does this approach gain the thickness needed, it creates a better damped structure too.
These chunky wooden panels are then shaped in a rather clever machine that can work in five directions – forwards, backwards, side-to-side and downwards. It’s capable of producing all manner of complex shapes such as that shown below – a Viva Utopia front panel.
Once all the cabinet panels are cut and machined into shape, they are glued together by hand. The whole assembly, minus the (usually) veneered side cheeks, is held in clamps until everything dries. It’s a time-consuming and labour intensive process thanks to the complexity of the cabinet construction of both the Electra and Utopia ranges.
Focal Scala Utopia in a brace (above); internal construction of Focal Electra 1028 (below)
After the cabinet has fully set, its outer surfaces have to be sanded down in preparation for painting. This is a laborious process: all the curved parts are done by hand, and the flat sections by machine. If this part isn’t done properly it would be impossible to get a good enough finish later on.
When the bare cabinets are fully prepared, they are primed and sanded again until the surface is smooth enough to apply the final coats of paint. This is a pain-staking process that requires every microscopic surface flaw to be corrected before final painting. Once painted the cabinets are polished (see Focal Electra 1028 below).
The construction of these speakers is such that the side panels are bolted on afterwards. These are prepared in much the same way as the cabinet panels but tend to be veneered. Focal uses a vacuum process that ensures even pressure is applied across the panel to ensure a good finish.
In addition, the Utopia range is customisable to any colour the customer wants. All they have to do is give Focal a sample of the colour they want and the company will match it. Popular choices are Lamborghini Orange and Porsche White. Below are shown the racks of panels ready to be fitted to the main speaker cabinet structure of Utopia models:
Once the cabinets are completed they are transported to Focal’s drive unit plant for completion. The larger Utopia cabinets are carefully packed in wooden crates for safe transportation (see below).
Unlike most rivals, Focal makes all its own drive units, including the units used in its in-car, pro audio and entry-level products. You can find out more about how the drive units are made in our second blog.
Written by Ketan Bharadia
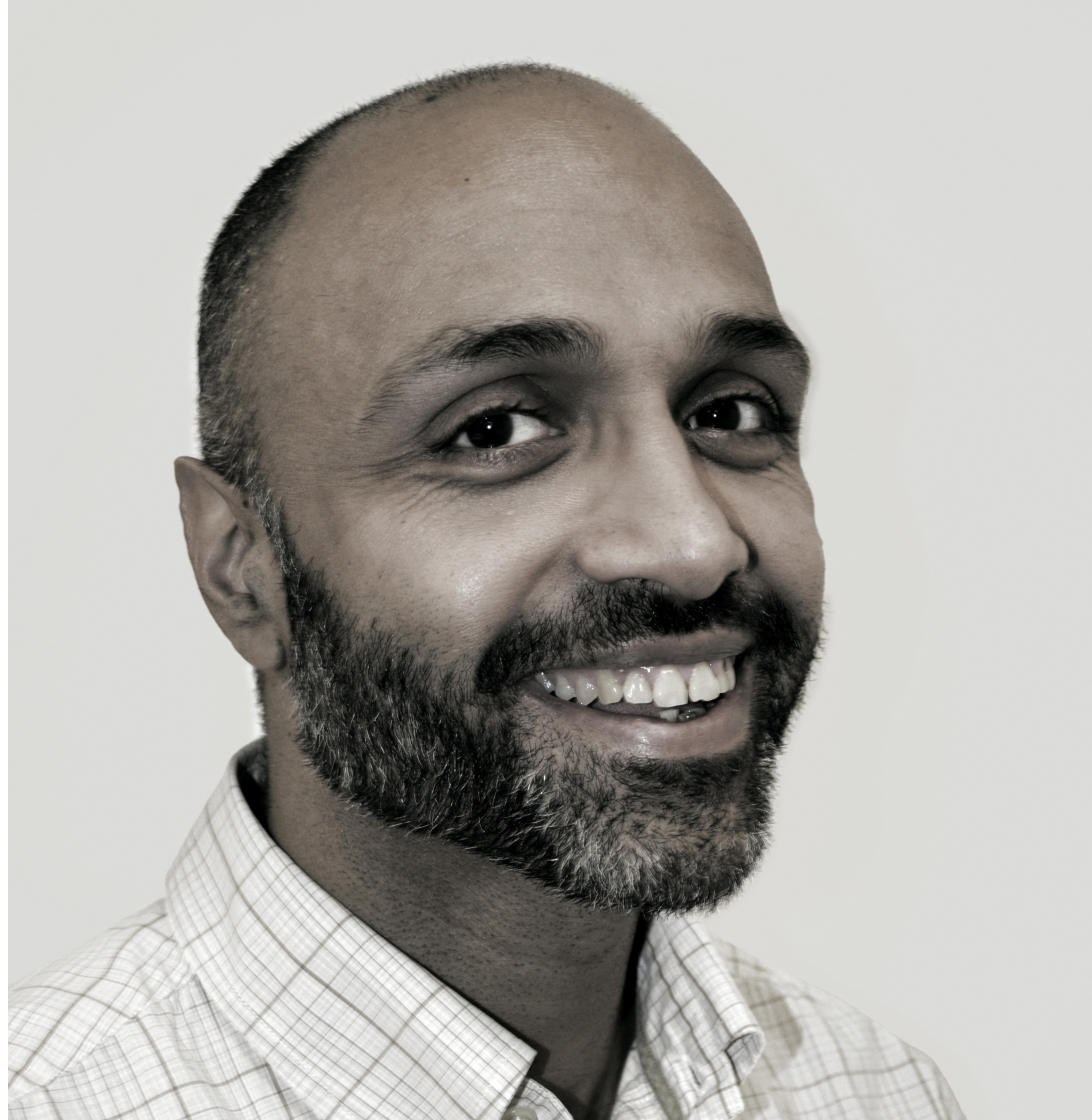
Ketan Bharadia is the Technical Editor of What Hi-Fi? He has been reviewing hi-fi, TV and home cinema equipment for almost three decades and has covered thousands of products over that time. Ketan works across the What Hi-Fi? brand including the website and magazine. His background is based in electronic and mechanical engineering.