The making of: Technics SL-1000R
Here's how, and where, Technics' premium turntables are made
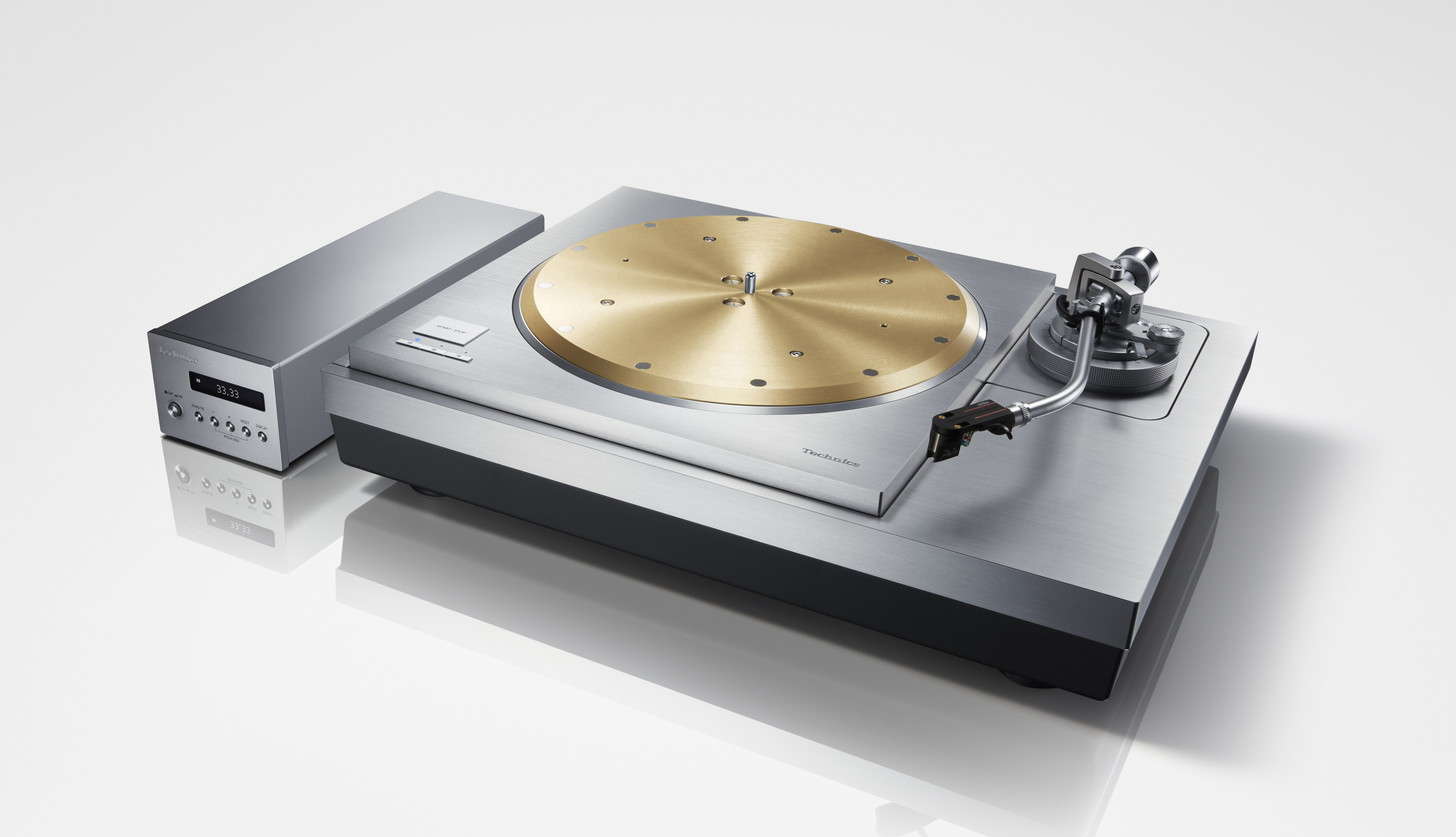
About 130km north of Tokyo is a small city called Utsunomiya. It’s home to a huge Panasonic factory that covers 60,000 metres squared and makes a variety of the company’s products from premium OLED and LCD televisions to set-top boxes. A tiny portion of this site, about a 60th, is given over to one of Panasonic's subsidiary brands - Technics.
Here, just 11 people manufacture Technics' high-end turntables and the ultra-high-end SU-R1/SE-R1 pre/power combination. The brand’s other, less specialist (and more affordable) products are made in another factory based in Malaysia.
The three complete record players, the SL-1200GR (£1300/$1699), SL-1200G (£2700/$3800) and SL-1000R (£13,999/$20,000), along with the arm and plinth-less SP-10R turntable (£7999/$10,000), are handmade by the factory’s most skilled staff.
Before anyone gets to build anything in this factory they have to go through an extensive training course and pass a number of skills tests that not only gauge dexterity but accuracy and speed too. The training lasts anything from three to five days. Only those that pass the toughest tests are allowed anywhere near the Technics products.
We follow a high-end SL-1000R record player as it gets built. Every deck starts off as a collection of parts carefully laid-out on a dedicated trolley. Each deck is made up of around 150 parts and is fully assembled by just one person. The company feels this approach is the best way to ensure quality levels remain high.
Each technician carefully follows the instructions on the facing display screen, making sure every part of the assembly procedure is followed to the letter. A checklist is completed at every stage to confirm each job has been done.
The complete construction takes around an hour and a half, and the factory produces up to five SL-1000Rs per day. In comparison the cheaper decks are far quicker to make, the SL1200G taking about an hour and the entry GR about 45mins. In terms of quantities, the factory makes around 15 and 25 of these respectively per day.
Get the What Hi-Fi? Newsletter
The latest hi-fi, home cinema and tech news, reviews, buying advice and deals, direct to your inbox.
Once the SL-1000R is fully made it is wheeled on a trolley – at just over 40kg it’s too heavy for one person to carry – to another station where the deck is set-up to be level and properly adjusted. This looks a tricky affair as far as the platter adjustment is concerned and laser measurement is used to ensure everything is spot-on.
Then comes the testing and listening. Each player is connected to test equipment to ensure wow and flutter levels (low and high frequency speed variations) are within tolerance, as well as ensuring that there are no problems with the internal wiring or overall construction. Every deck is also listened to with specific recordings to ensure everything sounds as it should.
Once the technician is happy with the measurements and sound – if they’re not it gets sent back up the line for assessment – the SL-1000R makes its way to the final quality control area.
Here, with the help of some very bright lights, another technician will check every surface of the deck to ensure that the finish and build are perfect. If they’re not, the SL-1000R will be sent back for reworking.
Only when the technician is happy is the player boxed for shipping. Be careful if you ever need to move this box, it weighs in at 52kg and is at least a two-person lift. We’re getting one in for review soon. We can’t wait.
MORE:
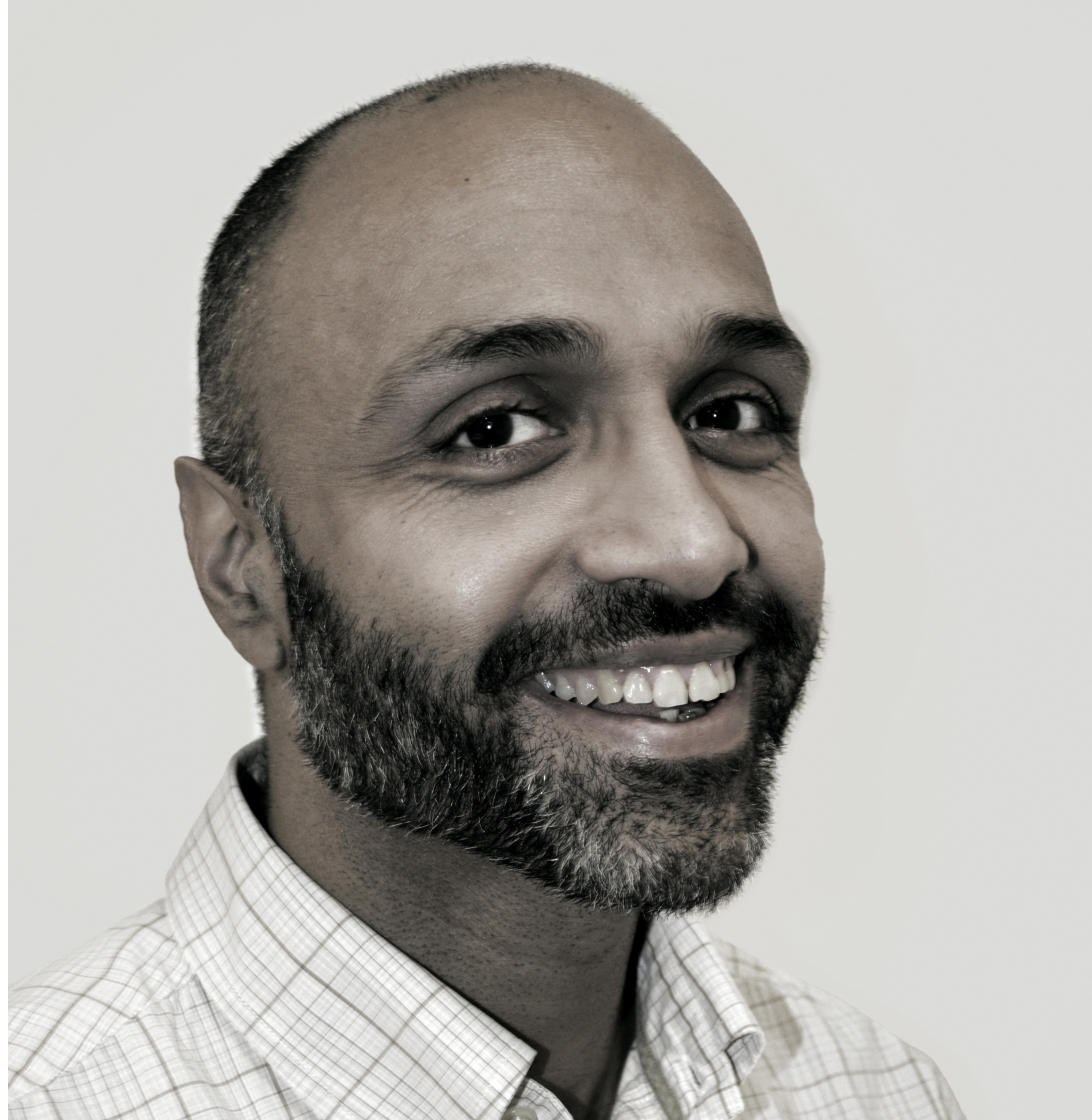
Ketan Bharadia is the Technical Editor of What Hi-Fi? He has been reviewing hi-fi, TV and home cinema equipment for almost three decades and has covered thousands of products over that time. Ketan works across the What Hi-Fi? brand including the website and magazine. His background is based in electronic and mechanical engineering.