KEF’s Jack Oclee-Brown: "The job of the speaker is simply to not get in the way"
Jack Oclee-Brown, KEF’s Head of Acoustics, tells us about early experiences in hi-fi, drive unit engineering and his mum’s singing
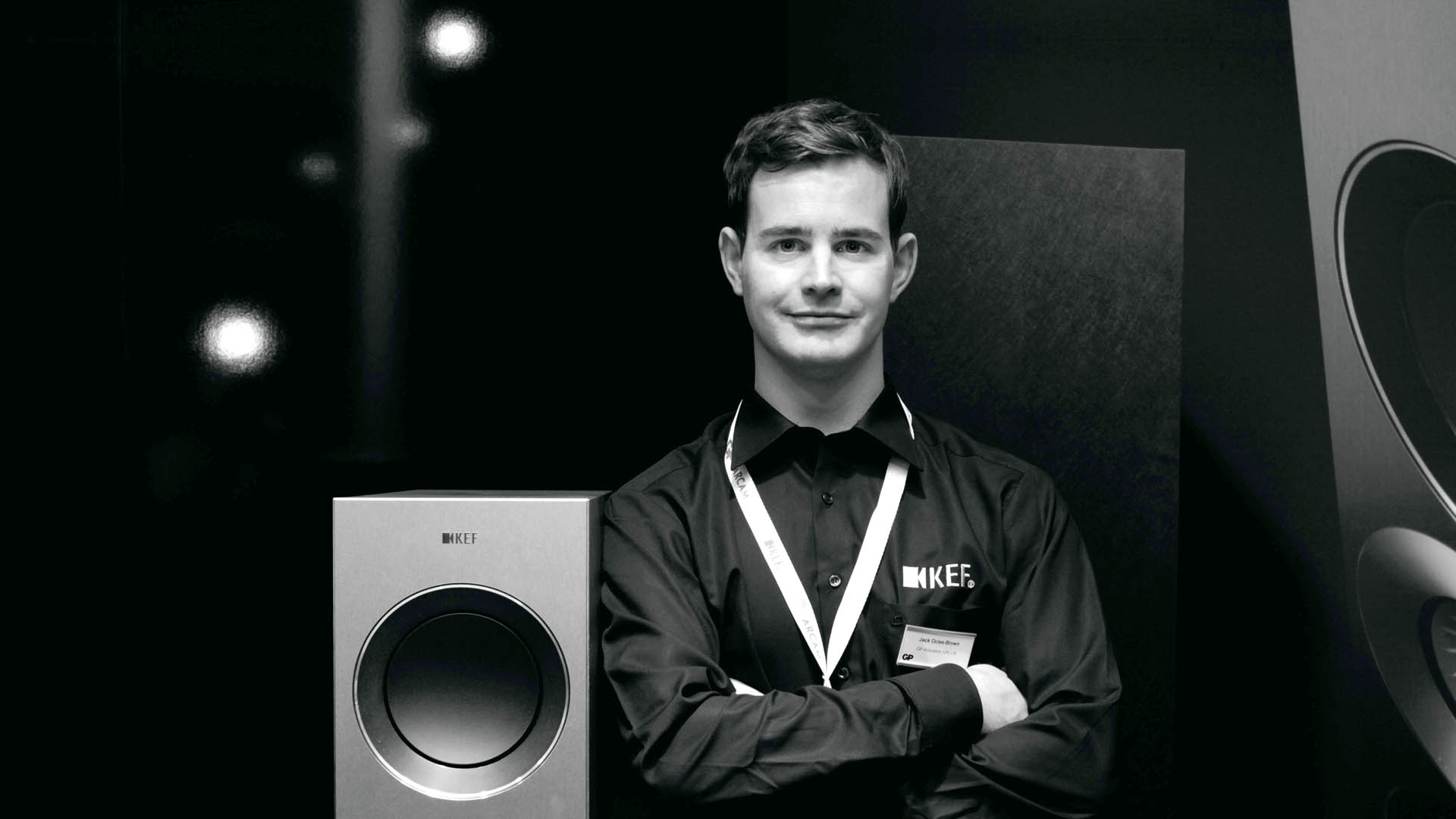
If you’ve heard any of the speakers KEF has made over the last decade or so, the chances are that Jack Oclee-Brown has had a hand in shaping them. Now the company’s Head of Acoustics, Oclee-Brown's work includes all the company’s recent star performers from the 50th-anniversary model, the LS50, to the high-end Reference 1 and class-leading R3s. We find out about his hi-fi journey.
What Hi-Fi?: How did you get interested in hi-fi?
Jack Oclee-Brown: My family is quite loud, and although we didn’t really have a hi-fi, when growing up there was always music around at home. My sister, brother and I all played instruments and my mother was, and still is, almost continually singing.
I remember finding an old record deck, some speakers and a few LPs in the attic one day and bringing the system down to my bedroom. I spent hours playing with it. This slowly became my hi-fi system.
One of my aunts heard that I was interested in speakers and gave me a pair from an old Sony system that she was throwing out to replace the ones from the attic. I remember being struck by how much better they sounded.
I had a very good friend who played bass and sang in a band at his school. We had a lot of common interests, especially in music. As we learnt more maths, physics and electronics at school both of us started to build equipment. Bill built himself a bass combo. I built a rudimentary mixing console and used it at one of his gigs.
Shortly after this I realised that speakers were really the thing that interested me most. Bill gifted me the book he’d used to design his bass combo and during the summer holidays I designed and built a better pair of speakers for my hi-fi. I tried to calculate everything according to the methods in the book, using driver parameters from the datasheet and lookup tables for the port tuning frequency. I had very little equipment to help me and not too much by way of woodworking tools. But after a few weeks working almost every day the end product was pretty good – and certainly a huge improvement over the old Sonys.
In sixth form, and now dead set on an engineering career, I studied Maths, Physics, Design and Technology, and Economics. Any topic in lessons that had the slightest relation to speakers or sound was carefully absorbed.
Get the What Hi-Fi? Newsletter
The latest hi-fi, home cinema and tech news, reviews, buying advice and deals, direct to your inbox.
By the next summer I was hungry to try again and designed and built another set of speakers. This time I did a much better job. I built a measurement microphone and preamp, used computer software to design the enclosure box, tune the ports and to simulate the crossover behaviour.
These speakers were much better than the first attempt and they came with me to the University of Southampton when I started my Acoustical Engineering degree at the Institute of Sound and Vibration Research (ISVR).
How did you end up at KEF?
During my second year at University I wrote to practically every loudspeaker company in the UK to ask for a summer placement – I remembering going through the manufacturers list in the What Hi-Fi? Buyer’s Guide to draw up a shortlist.
I also mentioned to one of my lecturers that I was looking for an opportunity and he made some enquiries for me. I received nothing for weeks but eventually got a call from Mark Dodd at KEF who arranged three months working at KEF R&D in Maidstone in 2002. At the end of the three months they asked me to come back the following summer, and they then offered me a permanent job when I graduated in 2004.
What does your job entail?
My job at KEF is to manage the research and development department in Maidstone. We are a small team of dedicated engineers and we develop KEF’s unique driver and system technology. It’s our responsibility to make sure that KEF products sound great.
We do engineering design work on upcoming products, research work to develop improved technology that could lead to better sound, and advise KEF’s product planning team on what will or won’t work acoustically in future products. We develop software to help us better simulate the behaviour of our loudspeakers and we also do research into how listeners perceive our products so that we can better understand how to improve them.
It’s my job to coordinate the team, prioritise our tasks and make sure we’re working on the right things to keep KEF producing new and exciting products.
What sonic qualities make an ideal speaker?
We’re trying to make speakers that are completely captivating and totally absorb the listener into the music they’re enjoying. Music is truly diverse, and as much as audiophiles like to moan, in most cases produced with deep care and attention to detail.
The job of the speaker is simply to not get in the way, not to show off, or stand-out, or distract. We strive to design neutral speakers that allow instruments and voices to sound natural, that don’t restrict dynamics or flatten the sound, that resolve the smallest of details, and that spread the sound into your room very evenly so you can enjoy the three-dimensionality in the recordings.
What’s the process of speaker development?
The starting point for any successful development is a carefully considered target, or design brief. This outlines an overview of what we’re trying to achieve. Things like, how big it should be, where it’s likely to be used, how it will be used and how much it will cost.
We will set a performance target at this stage too, and this is often done in relation to other KEF products or research prototypes. It’s then the job of the engineering team to come up with a system configuration to hit these targets. This would typically involve a fair bit of computer simulation, often some early prototyping, and typically some discussions with manufacturing teams to determine an engineering specification for all of the parts.
At the end of this stage we have an overview of the parts required in the product. For example, the sizes and arrangement of the drivers, the crossover frequencies between different sections, the internal division of the enclosure, the required driver characteristics, the size and location of ports etc. If it’s an active loudspeaker, we also consider connectivity, as well as the electronics and DSP requirements.
The detailed engineering follows, with every part fully designed and confirmed. This process can take a considerable time, particularly for complex parts like a Uni-Q driver to be fully designed, simulated and prototyped. The eventual outcome is a number of fully working prototypes that we can assess and listen to.
When we develop a new product we tend to pick out specific references to make comparisons – the model it will replace, the equivalent model from the range above, and often one of our high-end models too.
Is there an ideal material for drive units?
Ideally the loudspeaker driver should behave the same for any signal it receives. The trouble is that mid and treble signals require the driver to react extremely fast. The cone must be light and stiff to follow this fast movement or else it will bend. With all materials bending, resonance eventually occurs at some point. Typically the best materials, from a pure lightness and stiffness perspective, are the worst in terms of the severity of the resonances.
In addition there are other factors that have a huge effect on the cone or dome resonances – such as the exact geometry and the characteristics of the attached components, the surround, and voice coil mass and stiffness.
While there are certainly materials that are better than others, I don’t think that there’s a single ideal material that will give perfect performance. At KEF our approach is often to combine different materials together, each having complimentary properties. For example, a stiff and light aluminium cone with a rubber absorber at the neck. This approach can give combined performance that’s not achievable with a single material.
Why haven’t we seen a three-way Uni-Q?
The simple answer is because the drawbacks would outweigh the benefits. Uni-Q does an exceptional job of making two drivers blend into one coherent source. But it’s a very tricky arrangement that’s taken KEF years to perfect. We are totally committed to Uni-Q because we don’t think that there’s any other way to make the crossover between the midrange and tweeter invisible to the listener.
Technically this is because the acoustical wavelength is small at upper mid and high frequencies. You can’t get two separate drivers close enough together that they create a single source.
At lower frequencies wavelengths are longer and this makes it possible, with careful positioning of the low frequency drivers, to blend multiple drivers together successfully. So, for example, in systems like the KEF Blade, we can achieve a virtual point source over the entire frequency range but without needing a three-way Uni-Q.
What piece of design are you most proud of?
I think that it would have to be the Tangerine waveguide design on our current products. The original idea for a waveguide of this style came from Mark Dodd. It took us a while to understand the acoustics of this arrangement. The first efforts worked in simulation but couldn’t be manufactured perfectly.
In the end we came up with a brand new technique to generate the shape of the channels. It appeals to me because the shape was derived for its acoustics properties, but once we started seeing parts in 3D CAD we saw it was also something that had a really interesting and intricate geometry.
Measurement or listening? Which takes priority?
Our goal is to deliver the listening experience we’re looking for in a product. But if you never measure then you can only theorise about what you’re hearing in the listening room. The aim is to link the two together – to be able to measure just the right things so that you can say how good the speaker will sound. Or when you hear something you don’t like, to be able to go and find out in the measurements what’s going on. By getting the two tools working together you can make much better speakers.
What are your favourite KEF speakers?
I have a great deal of admiration for the loudspeaker engineering that KEF was doing in the late 80s. Very novel and carefully thought through work, with a fraction of the engineering tools available today. I’d say this is typified by the 105/3, which is packed with clever ideas and attention to detail.
I remember having such great fun during the development of the Concept Blade. Hours of simulation, hours of work on various prototypes– each one sounding better than the last. We worked for five years on that project.
I have a soft spot for standmount loudspeakers. In the right room, and on the right music, they can create a really personal listening experience that’s hard to beat. Just before I leave the office I sometimes sneak into the listening room for “just one song” and it’s always a pleasure to see a pair of Reference 1s waiting for me.
What about your favourite non-KEF speakers?
My dad had a friend with a pair of Yamaha NS1000s. It was my first proper taste of proper high-end loudspeakers and it stuck with me very clearly.
During the balancing of the 201/2 I remember getting hold of some Celestion Kingstons for comparison. A great example of a simple loudspeaker executed well – and one of the most inert loudspeaker cabinets I’ve ever come across.
There are so many different considerations in a loudspeaker, and designing a good one is a puzzle of how to focus on the things that matter most, whilst at the same time not having to make serious compromises.
I really admire products that come together with a clear objective and where you can easily understand what the engineering team were trying to achieve. It’s also refreshing to see and hear different approaches to those that you have chosen.
What are your favourite pieces of music?
I’ve become a big fan of the Philharmonia Orchestra. Some years ago I got into the habit of travelling up to their concerts at the Royal Festival Hall. To my ears they have the most wonderful tone, particularly in their string sections. Esa-Pekka Salonen conducting Sibelius Symphony No.2 in 2014 is one of the most remarkable things I’ve ever heard. Music means different things to different people, some music is for sharing, some for keeping. My favourite pieces are just for me to know.
What music do you use for testing?
I strongly disagree with the notion that a very good loudspeaker can only be used with audiophile recordings. Very seldom is a record made without great care and attention to detail. The style of recording, or the aims of the producer can sometimes be at odds with audiophile desires. Or the equipment used in the recording and mastering might not be up to the high standards we aim for. But an exceptional speaker, free from colouration and resonance with a natural timbre, will replay the recording more faithfully and with less artefact than a poor speaker.
When testing speakers a certain level of fidelity is required in the recording, but familiarity with the music is critical. In addition I find it extremely helpful to draw upon the opinions of others during critical listening decisions. Everyone has their own personal music taste, it’s important to test products with a wide range of material. And each of us listens in a different way with unique preferences and priorities in what we hear.
Describe the speaker hi-fi enthusiasts will be using in 20 years time
In the last 20 years, in many respects, loudspeakers have not changed much. The underlying driver and acoustic technology is very mature. Even so, I believe there’s still lots of opportunity to refine drivers and acoustic design to get better fidelity. A move towards more active designs could change things significantly over the next few decades.
What Hi-Fi?, founded in 1976, is the world's leading independent guide to buying and owning hi-fi and home entertainment products. Our comprehensive tests help you buy the very best for your money, with our advice sections giving you step-by-step information on how to get even more from your music and movies. Everything is tested by our dedicated team of in-house reviewers in our custom-built test rooms in London, Reading and Bath. Our coveted five-star rating and Awards are recognised all over the world as the ultimate seal of approval, so you can buy with absolute confidence.