Inside Timberworx, the speaker-building company you’ve never heard of
Meet the company that makes cabinets for some of your favourite speaker brands
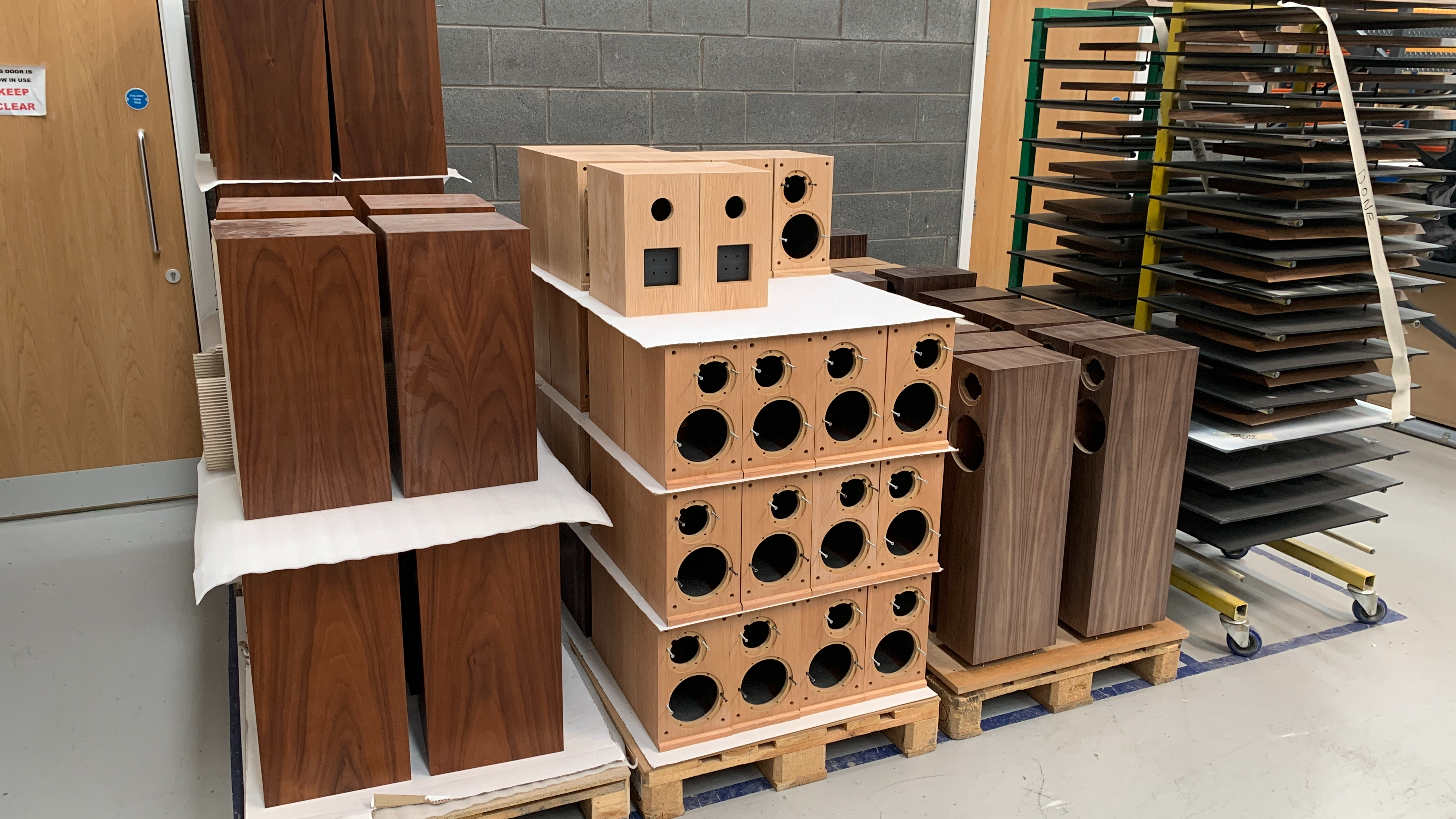
We wouldn’t be surprised if you’ve never heard of Timberworx. It isn’t a brand you’ll see at a dealer and it doesn't sell products online, and yet a surprising number of speakers that you probably know and love have passed through its doors.
Timberworx is a specialist speaker cabinet maker based in Sheffield, a city in South Yorkshire, England. It has been under Spendor's ownership over the last six years, and as well as building enclosures for Spendor speakers also makes them for the likes of ProAc, Neat, KEF, Linn and Mission, among others.
There are some big names among those 'others', but they would prefer that customers didn’t know that the building of their cabinets is outsourced to a third party, so we aren't permitted to mention their names... NDAs and all that. Given the investment, expertise and quality at Timberworx, it’s a reticence we can’t quite understand.
Back in the 1970s, there were a large number of cabinet makers in the UK building speaker enclosures not only for British brands but also international ones such as Acoustic Research and Sony. Gradually, that business migrated to Asia and in particular China. This led to a situation where very few cabinet manufacturing facilities remained in Europe, and that’s still the case today.
Timberworx is one of the remaining few and, thanks to careful planning and strategic investments, is now prospering at a modern 25,000-square-foot site in the technology-dense Advanced Manufacturing Park in Sheffield, next to large industrial units occupied by the likes of McLaren, Boeing and Rolls Royce.
There’s plenty of room for expansion if needed, and plans are already progressing to add extra facilities for Spendor in the same building. Timberworx currently has 50 employees who collectively build 3000-4000 cabinets a month, which is around four times as many as when Spendor first took over.
During our recent visit to Timberworx, we talked to Philip Swift, MD of Spendor (and the co-founder of Audiolab), to find out more about the speaker cabinet manufacturing process. It turns out that Timberworx mostly caters to those manufacturers that want high-quality cabinets in small to medium batches, i.e. tens to hundreds, rather than multiple thousands. The ‘Made in the UK’ tag is really important for many of those companies and helps the sales of their products worldwide.
Get the What Hi-Fi? Newsletter
The latest hi-fi, home cinema and tech news, reviews, buying advice and deals, direct to your inbox.
The 'inclusive' Timberworx business model
It might seem strange that a Spendor-owned company also makes cabinets for brands that would typically be considered rivals, but doing so is the only way to have the kind of production volumes that justify the huge investments in machinery and manufacturing technology necessary to turn out high-quality modern cabinet designs. The Timberworx business model can only work if Spendor doesn’t get any special treatment and is handled in the same way as every other customer.
The process of making a cabinet can begin with something as simple as a sketch with a basic set of dimensions or, more preferably, proper 3D CAD technical drawings. After this there follows a discussion between Timberworx and its client about what needs specific attention, and from there the production engineering plan is made. The process is trialed with the first prototypes and refined over numerous iterations until both parties are happy for production to start.
Cabinet making starts with raw materials, and as we walk through the production facilities we’re impressed by the sheer quantities of MDF, plywood and veneers involved. Swift is quick to point out that Timberworx only uses the more expensive, denser grade of MDF on quality grounds. The company doesn’t only deal with wood, as it is able to machine more specialist materials such as Corian, if required.
From MDF to objet d'art
The first step is to cut the wooden panels to the approximate size required and prepare the veneers that need to be applied. These veneers come as relatively thin stripes that have to be matched carefully and stitched together so that the sheet becomes large enough to cover a cabinet panel. The veneers are then bonded to the panels in a heavy-duty, multi-ton press.
Interestingly, the veneer is usually applied on both sides of the panel, even if one side won’t be seen. But we're told that this is to prevent that panel from warping as the temperature and moisture of its environment change over time.
The human touch
Next, they are put on one of Timberworx's CNC machines to profile the edges so that they can be formed into a box. The holes for inserts, terminal panels, ports and drive units are cut, as well as any specific grooves required for internal bracing if specified.
This is also when any damping pads are attached as well as metal inserts for bolts put in. Acoustic foam or fibre is also added into spaces that won't be accessible once the box is built.
Once that’s done, things move to the assembly area where the fully machined panels are ready to be glued together to form the box, and that glue is colour matched so as not to stand out. While Timberworx could assemble the enclosure using a machine, it finds that people give greater precision, particularly in tricky areas like corners and edges that have to be crisp and perfectly aligned.
Sand, spray, repeat
After allowing time for the glue to dry, these fully formed cabinets still need to be finished. The veneer has to be sanded in a two-stage process with a motorised abrasive belt that is used first to make the surface as smooth as possible and then to provide an initial coat of lacquer that is tinted or stained depending on the final finish option. Hand-sanding comes into the process to ensure that the surface and edges are as smooth as possible, with the cabinet then cleaned to get rid of dust and any unwanted residue.
But that is not the end (though we are almost there)! It then goes for final finishing which usually involves two or three repeat cycles of spraying and hand-sanding to get the desired result.
The almost-finished cabinets then go through an inspection process with any minor imperfections corrected by hand. It’s not a surprise that this needs to be done given the naturally variable nature of wood. If plinths need to be added, it is done at this point. The plinths themselves are machined, prepared, veneered or painted depending on whatever is specified in the design.
All that's left for the Timberworx team to do then is carefully pack the cabinets and strap them onto pallets ready to be shipped to the client, who then will assemble the complete speaker by adding drive units, crossover networks, wiring and anything else that’s required.
As we leave the Timberworx factory to take the train back to London, it’s hard not to be impressed by the operation and the care taken in making the cabinets. While the company has come a long way since its inception, it’s clear there is a will to keep on improving. We wish it well.
MORE:
The ugly truth behind hi-fi's growing infatuation with nostalgia
How is an iconic speaker resurrected for the 21st century? We asked JBL, Wharfedale and more
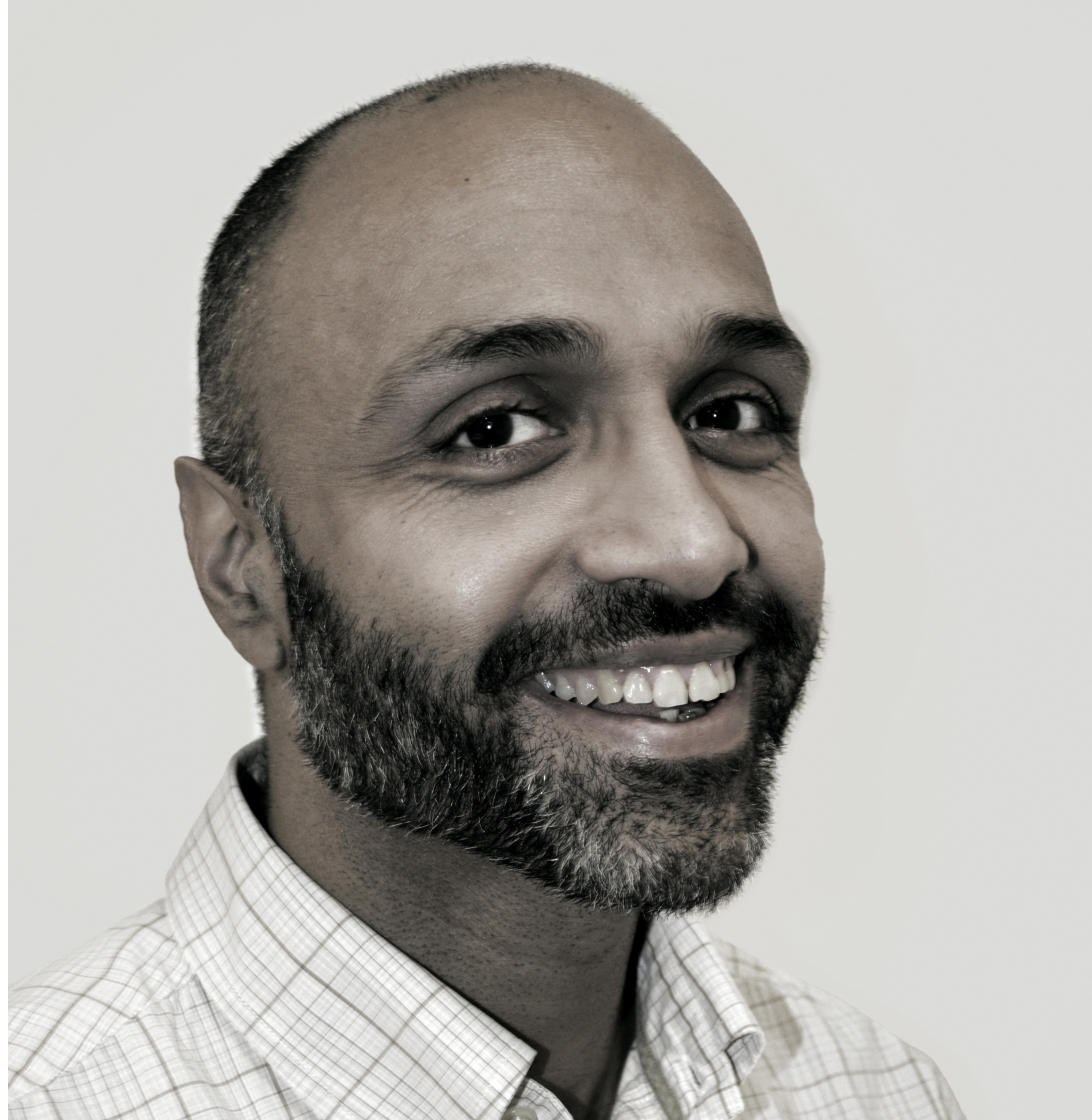
Ketan Bharadia is the Technical Editor of What Hi-Fi? He has been reviewing hi-fi, TV and home cinema equipment for almost three decades and has covered thousands of products over that time. Ketan works across the What Hi-Fi? brand including the website and magazine. His background is based in electronic and mechanical engineering.
-
nopiano They supply a wider range of manufacturers than I realised. And a great way for Spendor to find out what its rivals are made of!Reply -
Peter Farrow One is led to believe by marketing and messaging that speakers are hand crafted in house by their respective manufacturers.Reply
Now we find out their cabinets are made by a third party company and churned out by the dozen from a factory in Sheffield for numerous brands including Chinese companies such as Mission (IAG).
Its interesting that they openly admit that it allows Spendor to snoop on the designs of other cabinets.
So "Made In Britain" is now just a band-aid slapped on speakers because their cabinets were made in Sheffield by a third party. Its a shame especially for companies who really are qualifying for Made In Britain status now have this blemish on the "Made In Britain" logo to detriment of real "Made in Britain" products. -
LesterPJ Peter Farrow said:One is led to believe by marketing and messaging that speakers are hand crafted in house by their respective manufacturers.
Now we find out their cabinets are made by a third party company and churned out by the dozen from a factory in Sheffield for numerous brands including Chinese companies such as Mission (IAG).
Its interesting that they openly admit that it allows Spendor to snoop on the designs of other cabinets.
So "Made In Britain" is now just a band-aid slapped on speakers because their cabinets were made in Sheffield by a third party. Its a shame especially for companies who really are qualifying for Made In Britain status now have this blemish on the "Made In Britain" logo to detriment of real "Made in Britain" products.
Most UK companies will not be using enough cabinets to justify the cost of making them themselves. Manufacturing staff and machinery is only efficient if kept busy. So it would put up costs and the retail price.
What does it matter where things are made anyway? Its the design, materials and build quality that is important. As long as the factory's QC is strong enough then it makes no difference to the finished product whether its made at the company's own premises, in Sheffield or in India, China or Vietnam. Surely its the quality of the product and the retail price that is important not the location of the factory? (Slave/forced labour excluded.)
If the marketing is making something of where it is made then its just trying to make you buy / pay more for something due to your own prejudices. That's one of the jobs of marketing people. It makes no difference to the product. -
Peter Farrow Where something is made is extremely important. Especially if its claiming to be "Made In Britain" which is an official marque.Reply
British manufacturing and design is just about the best in the world and that is why companies are going to great lengths to present that as a feature as it worth money on the bottom line as well as a sign of quality.
Since you don't care where good are made, would you be happy buying Russian goods? -
LesterPJ I would not currently be happy buying Russian goods due to their invasion of Ukraine.Reply
My comments were about manufacture rather than design. There are many very high quality sub-contract facilities in many different countries throughout the world. Putting things together properly from a design is not a uniquely British talent. Many people from other countries can do this just as well as the British.
Anyway for most products the consumer doesn't buy factory direct. If, for example, I was buying a hifi product from a British brand I would expect that business to ensure the quality of that product whether they had manufactured it themselves or got someone else, anywhere in the world, to make it for them. My guarantee of quality does not come from the location of the manufacturing plant but from the desire of the brand owners to set the quality of product they want that brand to stand for and to take what actions that are necessary to ensure that the product meets that quality. If they should sub-contract to a factory that isn't up to it i would expect them not to put that product onto the market.
So where it is made (politics aside) shouldn't matter.
Along with some brilliant cutting edge stuff British manufacturing is littered with examples of factories in Britain doing poor assembly. Made in Britain can be of high quality but it is not guarantee of it. -
Peter Farrow Where it is made is critical. You can't seperate the politics from the manufacture when talking about China and Russia. The mindset of the places you mention is to do it cheaply as possible, its a way of life for those cultures and its impossible to get consistant quality. Furthermore a few internet searches will enlighten you to the poor pay, long hours, no workers rights and terrible human rights of places like china. It endemic in the manufacturing for such states to do it cheaply and make the biggest margin possible for the owners.Reply
The concept of copying and ripping off is second nature. Taking British brands and moving all the manufacture to the far east, trading on the British names of former British brands with no DNA of the original design or mindset left in anyway.
Personally I find that loathsome, coupled with the way the workers are treated and the regime they suffer, means buying those products you are financially supporting that process at the same time killing UK manufacture.
If what you say were true about it doesn't matter where its made, why are all these chinese brands sticking half baked union flags on their products and pretending its still British? The answer is obvious, it really does matter and it matters alot to most people.
You're right in that buying British won't guarantee quality but in Hifi circles it really does guarantee it, because the true British brands couldn't survive against the unfair advantage of basically free labour, no green taxes etc that chinese manufacture has by comparison. The only way you can survive is being much better than the eatern offerings because costs are exponentially higher.
Most chinese built manufacturers are so desperate to convey the illusion of British made they put union flags on their products and in tiny writing underneath "Made in PRC" the name is so toxic that dare not mention it directly.
If I were a betting man I would bet with amost certainty that a 100% British made piece of hifi will be infinitely better than those churned out in the eastern sweatshops with a faux union flag on them.
If you expect a dealer to guarantee the quality of a product you are naively mistaken, the industry doesn't work like that. This is exactly the point the eastern manufacturers don't really care about the quality they want the cash and they do just enough to keep it flowing, they consider their products disposible and to them they are because they cost virtually nothing to make, so even if the QC is terrible they can just ship replacements until one that can outlast the warranty is delivered.
Nothing more, nothing less.
Where is made for hifi is literally the be-all end-all of the industry.
I wouldn't want a Bentley made in China, but it seems you would be ok with that.
Its a bit like buying a house, three most important things, location, location and of course location.