7 of the best British hi-fi innovations and technologies
KEF MAT, Continuum, current dumping, flux capacitors (...OK not the last one)
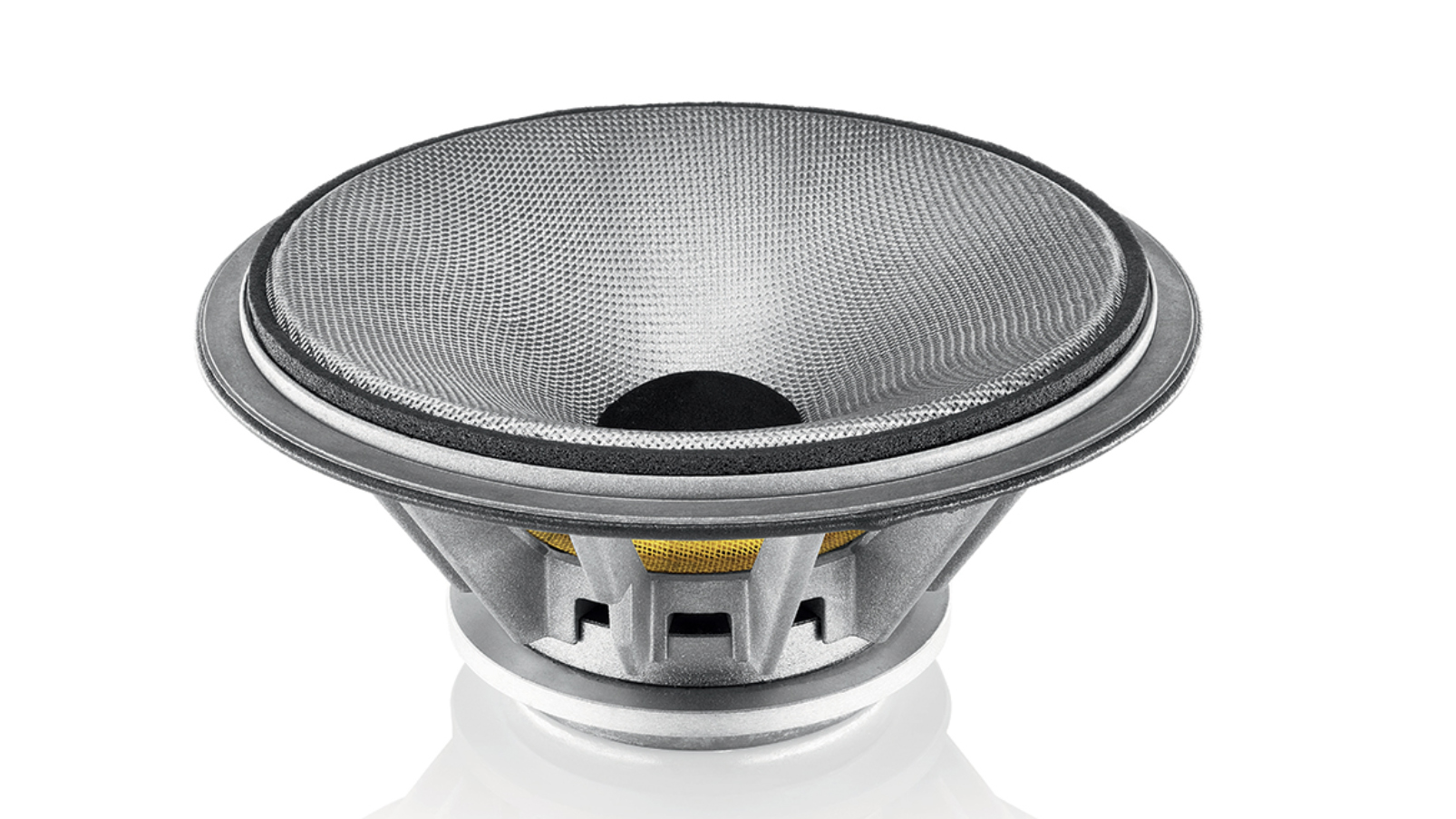
Britain has always been a nation that prides itself on its engineering and science pedigree, which is why it’s no surprise that it’s been the birthplace of some of the most interesting innovations in the hi-fi space.
This is why if you jump over to our best British speakers guide, you’ll see it’s absolutely rammed full of innovative products with more than a few patented technologies on show that can easily be counted. It’s also why, if we were to list every amazing British invention we’ve experienced reviewing in hi-fi over the past near-50 years, this article would read more like an encyclopedia.
Instead, we’re going to focus on the biggies that our team of experts personally list as their hallmarks for British hi-fi innovation. This list is part of What Hi-Fi?’s British Hi-Fi Week 2023 – a seven-day special event where our team of audio experts celebrates the best of British hi-fi past and present. Make sure to follow us on social and let us know if you think we’ve missed any key British hi-fi inventions off this list.
1. KEF MAT
KEF’s Metamaterial Absorption Technology (MAT) first appeared in 2020 on the What Hi-Fi? Award-winning KEF LS50 Meta standmounter speakers. The MAT technology is designed to help speakers cope with the unwanted sound that comes off the back of an aluminium tweeter dome so they don’t distort the unit’s forward output.
The MAT is a circular, plastic,”maze-like” structure that sits behind the tweeter. The specifics of the maze depend on the speaker, but effectively, the design means the rearward sound from the tweeter (such as in the LS50 Meta) feeds into a plastic circular maze element that is roughly the size of a hockey puck. The element is layered and made up of 30 tubes, each of which has been tuned to absorb a different frequency (from around 600Hz upwards). According to KEF, this MAT technology helps absorb “99%” of the unwanted distorting sound waves that radiate from the cone's rear into the cabinet.
This is important as distortion is a key issue on a lot of speakers, and many manufacturers attempt to get around this issue by using damping material to absorb the sound waves from the back of the dome. In our experience, some sound energy always bounces back through the driver to add distortion.
There have been other attempts to get around this issue, but the reason we’ve flagged KEF MAT over them is the innovative way it’s been designed and how well it works. Since we tested the LS50 Meta, our team of experts has consistently been impressed with just how well MAT works in the speakers, with our reviewers reporting:
Get the What Hi-Fi? Newsletter
The latest hi-fi, home cinema and tech news, reviews, buying advice and deals, direct to your inbox.
“It looks like the Metamaterial technology really works. These new KEFs sound so much cleaner and more sophisticated than before, particularly at higher frequencies [...] Large-scale dynamics are handled well and there’s a good amount of muscle for a speaker of this size. These are refined and composed performers that rarely sound stressed unless volume levels are high.”
This was a key reason we gave KEF’s MAT a What Hi-Fi? Innovation of the Year Award when it first came out. It’s also why we’re super happy it’s continued to be used and rolled out to other KEF speakers, such as the Award-winning LS50 Wireless II and the company’s updated R Series.
2. Quad electrostatic technology and 'current dumping' amps
Quad (an acronym for 'Quality Unit Amplifier Domestic') was founded by Peter J. Walker in 1936 in London, but the firm had to relocate to Huntingdon in Cambridgeshire in 1941 following the bombing of the capital during World War II.
In 1956, Quad unveiled the first true full-range electrostatic loudspeaker. Known later as the ESL 57, it used a very light plastic film as a moving diaphragm between two charged plates. Compared with moving-coil loudspeaker designs of the time, the ESL 57 marked a huge step up and remained in production, virtually unchanged, for almost 30 years.
1975 saw the arrival of the Quad 405 ‘Current Dumping’ Amplifier. It was the same year that Peter Walker told Wireless World magazine: "An audio power amplifier is required to produce an output signal that differs from the input signal in magnitude only. It must therefore have occurred to every circuit designer that it should be a simple matter to take a portion of the output, compare it with the input to derive a error signal. It is then only necessary to amplify the error signal and add it to the output in the correct amplitude and phase to cancel completely the distortion of the primary amplifier."
Walker put this theory into practice using two amplifiers per channel, where the first stage ‘error’ amplifier was low powered but very high quality, and the second high powered but of lesser audio quality. (As you may know, it’s extremely difficult to achieve very low distortion in high-powered amplifier stages.) He designed a way to compare the high-powered output with the original audio input and derive the necessary error correction signal to inject into the audio path – and crucially achieved a very low distortion figure, even at much higher power levels.
In essence, Current Dumping is a way of combining the sonic purity of Class A amplification with the much more efficient Class AB.
Sound a tad complicated? That was never Walker's intention, as evidenced by his famous quote: "The perfect amplifier is a straight wire with gain". The idea that nothing should be added or subtracted from the original signal to leave you with a bigger version of it at the end is the best summation of the perfect amplifier we can think of.
Walker never said he'd achieved this, mind, despite the fact that Quad was given the Queen’s Award for Technological Achievement for the Quad 405 in 1978. Nevertheless, his remarkable circuit topology remains one of the few truly original amplifier designs – and it still features in Quad products today.
3. KEF Uni-Q
KEF's website proudly states that of the many landmark innovations the company has pioneered, arguably the greatest of all is the Uni-Q point source driver array. With its even off-axis dispersion, built following twenty years of innovation, research and development, the Uni-Q driver array boasts the ability to let sounds come at you in a whole new way.
How, exactly? Unlike conventional speakers (where the tweeter sits above the midrange driver), the Uni-Q unit is two drive units in one coincident assembly – the tweeter is situated slap bang in the middle of the midrange driver, like the bullseye of a dartboard. Thus, midrange and high frequency sounds come from the same physical 'point' in space.
KEF says this configuration also offers a wider dispersion and does away with the traditional notion of a sweet-spot for listening, because the projection of sound is more even across the frequency range and less susceptible to beaming and lobing in the vertical plane.
Does it work? You might say – have a quick glance over our KEF reviews. But KEF doesn't have time to rest on its laurels. For its most recent (and What Hi-Fi? Award-winning) LS50 Meta, the Uni-Q driver array has been reworked, taking in all the refinements that KEF has developed over the past eight years and adding something new in the form of Metamaterial Absorption Technology (MAT).
MAT is KEF’s way of coping with the sound that comes off the back of the 25mm aluminium tweeter dome. In a conventional design, this sound usually fires into a chamber behind the dome where it is mostly absorbed by damping material. But some sound energy always bounces back through the dome to add distortion.
Here, the tweeter still sits in the throat of the mid/bass unit, but the rearward sound feeds into something about the size of a hockey puck that looks like a plastic circular maze. It is layered and made up of 30 tubes, each tuned to absorb a different frequency. KEF claims that, once combined, the tubes absorb a wide range of frequencies – from around 600Hz upwards – much more effectively than alternative methods. The result? Cleaner, less distorted highs.
4. dCS Ring DAC
OK so it doesn't look like a cute piece of jewellery but, as is often the case in engineering, there comes a point at which the performance of an existing technological approach cannot practically be improved. When this happens, progress means trying something different. And that, says the Cambridge-based digital specialist dCS (Data Conversion Systems), is essentially what happened when it developed the Ring DAC.
Although off-the-shelf silicon DAC chips can be bought for relatively little online, dCS wanted more than someone else's best efforts.
So dCS engineers did it themselves. The Ring DAC is a bespoke digital signal processing engine designed by and unique to dCS. This DAC (early model pictured above) is a clean-sheet solution running code written and regularly refined by the firm. It uses a network of FPGAs (Field Programmable Gate Arrays) programmed to run dCS firmware and handle all digital filtering and digital-to-analogue conversion.
Why go the long way around rather than buying in from reputable semiconductor suppliers? In 2014, dCS director of product development, Chris Hales, said, "Because we’re in control of the digital signal processing we can improve it. For example, the mapping algorithm – which is pretty crucial to the way the Ring DAC works – is something we change if we see fit. The filtering is completely under our control, so we’re not at the mercy of what’s in the chip that you buy, we can change it arbitrarily to whatever we want. We can even do that retrospectively and put that into products already into the field.”
Doing a digital converter the dCS way is far more expensive than buying in off-the-shelf DAC chips, but the results are undeniable – dCS DACs sound unlike anything else on the market because, well, that really is what they are.
5. Bowers & Wilkins Continuum drive units
If T. S. Eliot had written a possum's book about practical hi-fi (rather than cats), the opening line might read: "The making of midrange drivers is a difficult matter, it isn't just one of your holiday games."
The issue for any speaker manufacturer is the delicate dance between lightness (read: agility, speed) and rigidity (accuracy in movement) which makes perfect sense when you consider that the movement of the speaker cones generates the sound.
Nano-carbon fibre, sand-filled ultra-thin aluminium, Beryllium DLC (whereby a layer of 'Diamond Like Carbon' is deposited on the diaphragm surface using chemical vapour deposition to boast "diamond-like" strength) are all material solutions offered by hi-fi's greats. The aim, of course, is increased rigidity, transparency and accuracy.
So what did Bowers & Wilkins do? Well, if you're not completely happy with the minerals nature has supplied, you go back to the drawing board and create something new. Traditionally, Kevlar was the material of choice for B&W's midrange and bass drivers (a heat-resistant and strong synthetic fibre first used in the early 1970s as a replacement for steel in racing tires) but the company now uses its own material, dubbed Continuum. Marvel fans might be thinking of Wolverine's skeletal enhancement, Adamantium, or even Vibranium (only mined in Wakanda) right now – and that's actually fine by us. It's that good.
Bowers & Wilkins claims Continuum reduces the degrading effects of the vibrations of the mid/bass drivers, resulting in a cleaner sound with less distortion. Its inclusion has trickled down from B&W's flagship 800 Diamond series and happily you'll now find it used across all of the company's latest speakers. Do we like it? We do – just have a look at our Bowers & Wilkins reviews.
6. Acoustic Energy AE1's all-metal drive units
Being consistently successful for more than 30 years isn’t easy, but the Acoustic Energy AE1 Classics managed to handle it with aplomb. If it's a set of standmount audio-industry game-changers you're after, this is the pair we'd guide you towards.
The AE1s used an unusual-for-the-time all-metal drive unit line-up, twin forward-firing ports and a cabinet lined with plaster (designed to not only minimise the build-up of internal standing waves but add damping, too). The result was a sonic presentation packed with stunning dynamics, excellent detail and surprising authority – just as long as your partnering system had the required quality and muscle.
They’ve evolved over time, of course; the 2006 20th anniversary version featured cabinets that were glossier on the outside and thicker on the inside, but they were still lined with plaster – not everything changes.
The latest (and rather splendid) AE1 Active still features the pure piston ceramic aluminium cone technology we're celebrating here, now in its fifth generation. It offers exceptional stiffness without weighing the speakers down too much – and it all started in 1987.
At launch, Acoustic Energy’s first-ever 'mini-monitor AE1' speakers cost big money (about £700, which is getting on for £2000 in today's money) but they also shattered perceptions of what small speakers could do. A year later, in 1988, the company released the larger AE2s. These featured pretty much the same technology, but the cabinet was about a third bigger in each direction and packed in two of the 9cm alloy mid/bass units with three reflex ports.
In many ways, the AE2s were better than their smaller siblings, including delivering more powerful bass performance and greater authority – but they lived forever in the AE1s' shadow, probably because they lacked the surprise factor of the smaller speakers.
7. Wilson Benesch A.C.T. One's use of carbon fibre
Behold, the Wilson Benesch A.C.T. One speakers as they appeared in What Hi-Fi? magazine in 1999 (when we partied like it was, because it genuinely was).
Sometimes, a product sets a company's engineering template, and these floorstanders did just that for this 1989 Sheffield audio start-up. You'd think the engineers might have tried steel, but no.
Wilson Benesch turned heads back in 1991 with its first products, the imaginatively titled Wilson Benesch Turntable and its partnering tonearm, the A.C.T. One. Those initials stand for Advanced Composite Technology, and carbon fibre is at its heart. The deck used the material in its sub-chassis and the arm flaunted it in a beautifully shaped armtube, the impressive rigidity, low mass and good self-damping giving them quite the edge over contemporaneous rivals.
Even today, the use of carbon fibre is considered somewhat novel, but back then there were just three other UK companies capable of producing the composite parts: Lotus Racing and two specialists working for the Ministry of Defence – high company for a fledgling hi-fi brand to keep.
Rather than going the predictable release-a-more-affordable-record-player-follow-up route, in 1994 Wilson Benesch surprised us yet again with the A.C.T. One floorstanding speakers, this time grabbing headlines thanks to the use of curved carbon fibre flanks.
Even by modern standards, these towers are hugely capable, which is testament to the quality of engineering involved. In 2019, we reviewed Wilson Benesch’s latest entry-level standmount speakers, the Precision P1.0s (£5995, $8800), and comparing the two models was fascinating. It’s no surprise that the newer design is the more revealing and insightful – but that doesn’t stop us admiring the originals, the template from which all of Wilson Benesch’s subsequent designs are made.
Both are transparent and detailed performers, capable of delivering sound in an insightful, and musical manner – not a bad legacy for a firm that started out making turntables.
MORE:
What Hi-Fi? launches British Hi-Fi Week 2024 – fresh reviews, retrospectives on classic amps and more
Our picks for 9 of the most underrated British hi-fi products we've ever tested
Read up on the best audiophile headphones: ultimate high-end headphones
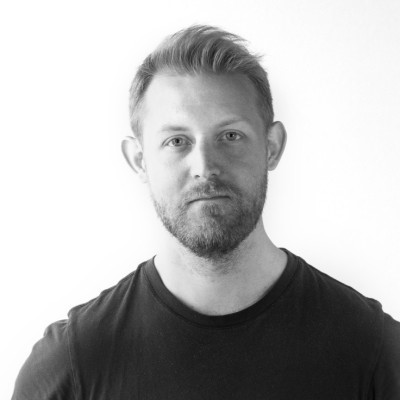
Alastair is What Hi-Fi?’s editor in chief. He has well over a decade’s experience as a journalist working in both B2C and B2B press. During this time he’s covered everything from the launch of the first Amazon Echo to government cyber security policy. Prior to joining What Hi-Fi? he served as Trusted Reviews’ editor-in-chief. Outside of tech, he has a Masters from King’s College London in Ethics and the Philosophy of Religion, is an enthusiastic, but untalented, guitar player and runs a webcomic in his spare time.