Behind the scenes at the home of Linn
We take a trip to Linn's HQ in Scotland to get an inside look at the hi-fi company's factory.
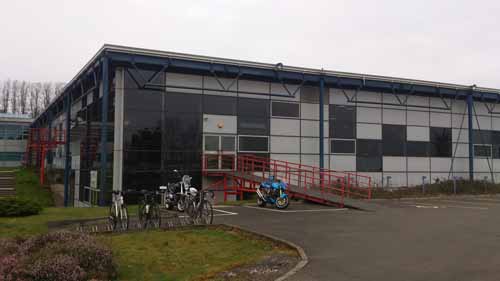
Linn is one of the stalwarts of the British hi-fi industry. Taking its name from a local park (the second biggest in Glasgow) Linn was founded in the early ’70s and started off with just one product – the legendary LP12 turntable.
Since then the company has developed an impressively comprehensive product range. It starts with high-resolution Studio Master recordings, continues through cutting-edge streaming products and finishes with a surprisingly varied selection of speakers.
Linn hasn't forgotten its roots, though. Forty years on, the company still makes the LP12, albeit in a much developed form – the Linn Majik LP12 for example.
It’s been quite some time since we've visited Linn, so we jumped at the chance when the invitation came. And we’re glad we did – its facilities are impressive to say the least. Linn’s factory stands alone, in what can only be called a field.
It’s an impressive building, designed by the Richard Rogers partnership, and has been notably expanded since the company moved in back in the late ’80s.
So isolated is the factory from other industry that the closest neighbours are a herd of cows.
Isolated it might be. Out of touch it certainly isn't. Linn is now one of the largest specialist hi-fi manufacturers in the UK, employing around 150 staff. And of those almost a third are engineers. That’s an unusually high figure, and says much for how highly the management values good quality engineering.
The latest hi-fi, home cinema and tech news, reviews, buying advice and deals, direct to your inbox.
The company tries to make pretty much everything in-house. Where it can’t, with things such as speaker cabinets – there are no wood-working facilities on-site – it uses a small group of trusted outside suppliers. As far as possible, the range of suppliers is kept to a minimum, to ensure Linn remains in control of its production.
Unusually for a hi-fi company, most of the metal work is done in-house. The raw material arrives as flat sheets, then goes through a series of processes. Holes are machined, and the metal sheets are then bent, cleaned and powder-coated. The thickness of the casing varies according to the product range: the entry-level Majik series has a 2mm thick lid; the higher-end Akurate's is twice that.
Many of the machines are as high-tech as you could wish, but some processes require something more traditional. Screen-printing, for example.
Here, the process is surprisingly old-fashioned: note the domestic-looking oven (below) that helps the drying process.
While the casework is being made in one part of the factory, the electronic circuit boards that fit inside are made in another. One of the messages consistently reinforced throughout our visit was Linn’s determination to have as much control as possible over the production process.
To that end, the company doesn’t buy in fully populated circuit boards in the way most rivals do. Linn does the job itself, with a collection of some pretty impressive machinery. Most of the components are surface-mount units. These are tiny, some barely bigger than a pin head, and so can’t really be soldered by hand.
The process starts with this stencil.
This stencil tells the machine where the components are going to go. A special paste is put in specific places so that when the circuit board is populated by the machine, the components stay in place. There’s a visual check – done by person - before the baking process locks everything in place.
Of course, there are always going to be larger components needed in hi-fi gear, so once these surface-mount components are fixed in place, other parts are added by hand, and soldered using another machine. The circuit boards are preheated so that they don’t get damaged by thermal shock when they come into contact with the solder.
On a busy day the company can use as much as 6kg of lead-free solder.
Once the boards are built they are tested in specially made jigs. These test not only the connections but also the software. Each product has its own specific test module. It's very impressive, but there is the look of a torture rack about them…
Once the parts are made they are put into storage until the final build. At this point one person is responsible for putting the circuit boards and casework together. That individual will also put the finished unit in its packaging for sale. Linn believes this responsibility will ensure higher quality. It also makes tracking any problems easier.
Most of the Linn building is dominated by manufacturing, but the company has taken the unusual step of building a showroom too – though 'showroom' is understating things somewhat.
The Linn Home is a deeply impressive area that aims to show that high-quality hi-fi and a smart domestic environment can go hand-in-hand.
The Linn Home is made up of six main areas: a lounge, dining room, bedroom, study and bathroom, and shows various Linn set-ups neatly integrated into the environments. It’s thoroughly impressive in its execution.
Before we finished we were treated to Linn’s top system...
This active Linn Klimax set-up features four 500-watt mono blocks per side and is fronted by the company’s top-streamer and the latest spec LP12 turntable. The whole lot is yours for a touch over £130,000.
MORE: Read all about the new Linn Akubarik active speakers
MORE: See all our Linn product reviews
Written by Ketan Bharadia
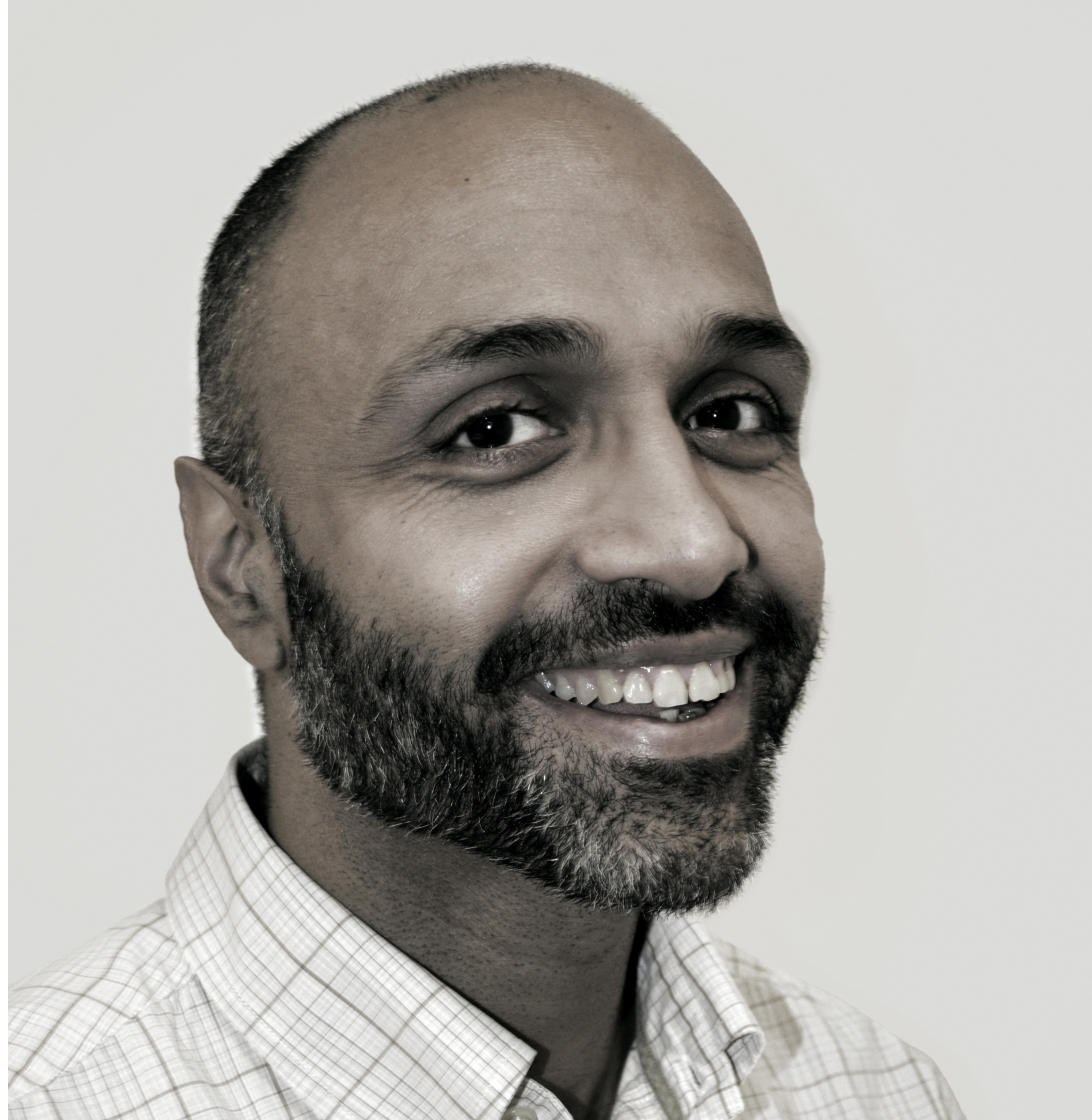
Ketan Bharadia is the Technical Editor of What Hi-Fi? He has been reviewing hi-fi, TV and home cinema equipment for almost three decades and has covered thousands of products over that time. Ketan works across the What Hi-Fi? brand including the website and magazine. His background is based in electronic and mechanical engineering.