Ask The Industry: hi-fi engineers weigh in on the value of 'running-in'
A priceless or pointless exercise?
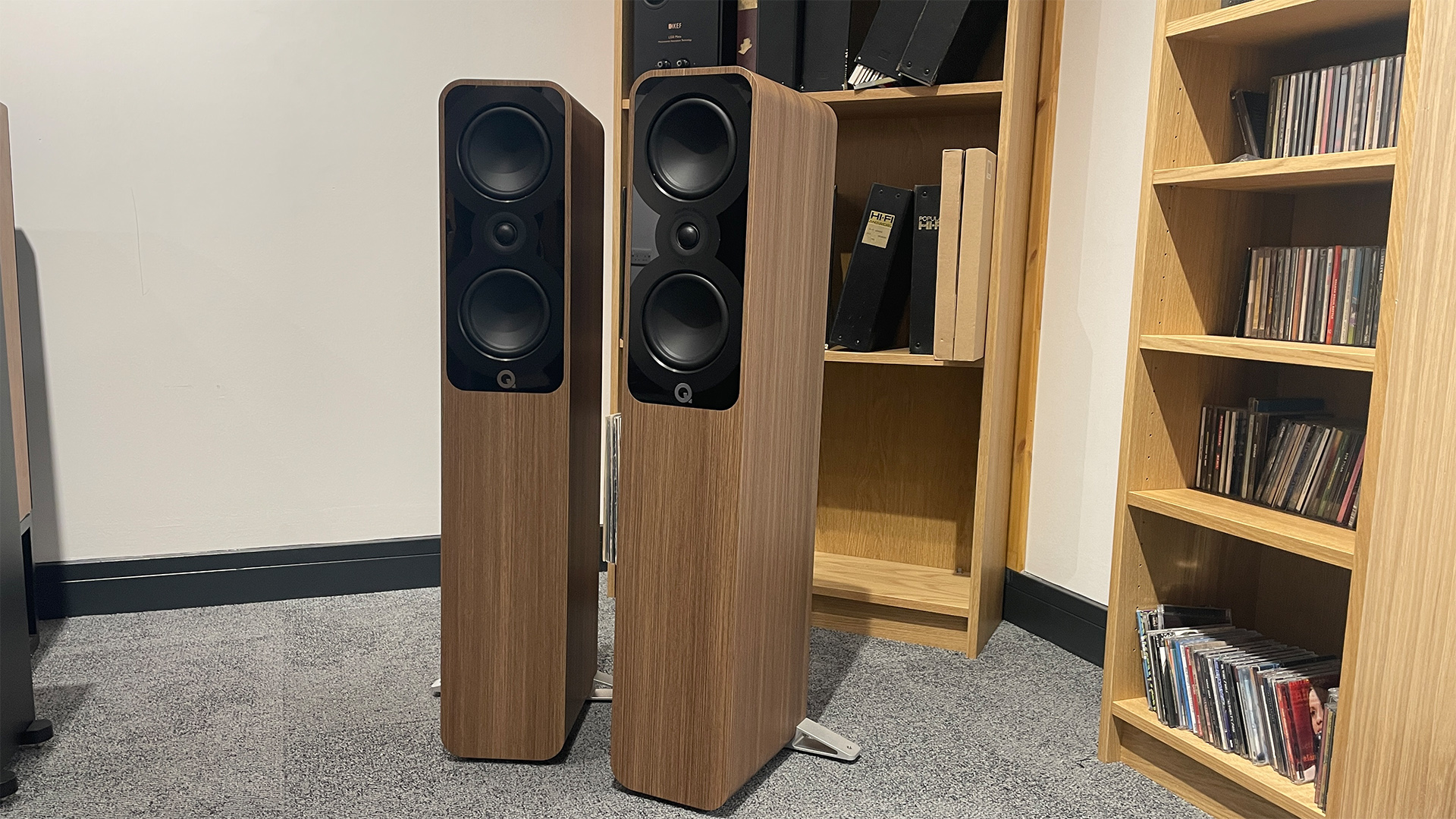
So you’ve just snuck some new hi-fi kit into your house and have wired it up to your system (being careful to hide the empty cardboard boxes of course). You’ve lined up your favourite album of 2024 (also a covert household purchase) and are ready and eager to listen to how much better it now sounds compared to yesterday and congratulate yourself on your latest (secret) purchase. But between set-up and performance scrutiny is a process that will undoubtedly irk the impatient but could prevent confusion if the kit doesn’t sound as you remember it from the demo room, or as you've read about in the reviews. Yep, we’re talking about ‘running-in’.
You’re probably familiar with the phrase (also referred to as ‘breaking-in’ or ‘burning-in’), if not in relation to hi-fi than perhaps a car, and it essentially refers to an initial period of use whereby the moving parts begin to work and stabilise in their forever environment, during which a last little bit of shifting could occur.
Just as a car shouldn’t be driven like a boy racer in the first miles of its life while the piston rings are still settling into the engine's cylinder wall and the brake pads and discs are adjusting to one other, hi-fi performance shouldn’t, according to popular thought, be taken as gospel until all of the moving parts have bedded in. For this reason “it’s essential to run in quality hi-fi, and not to judge it beforehand” as an engineer told What Hi-Fi? when we last broached this topic in 1994. Indeed, it’s something we have habitually done with every review product that has passed through our doors in the past four decades. When we used to run Supertests in What Hi-Fi? magazine of several (sometimes as many as 10) products at once, you can imagine how many cables, plug sockets and, in the case of headphones, multi-way splitters were involved to run them all in efficiently!
Thirty years later, has the school of thought changed? We asked a number of engineers in the industry for their thoughts on running-in...
The settling of mechanics
“There's no argument as far as we are concerned,” says Stephen Oakes of Neat Acoustics, and “it’s pretty clear cut” says Cambridge Audio’s engineering team – loudspeakers benefit from being run-in due to their physical and mechanical nature. “Loudspeakers straight out of the box will certainly sound ‘tight’ and far from the relaxed performance that is desired,” says Peter Comeau of the IAG Group. And Oakes affirms that “this is audible and measurable”.
Why? Well, firstly, drive units are made up of moving parts that are stiffer than intended when new and unworked. “The most obvious thing is that speaker bass cones and, to a smaller degree, tweeters move, thus moving air,” says Paul Mills of Fyne Audio. “It takes a while for the speaker surround, which is often rubber, and the rear fabric suspension to ‘ease up’”.
You then have the spider that makes up the majority of the total compliance of a woofer. This, says Oliver Thomas of PMC, “will have various coatings to optimise its mechanical and acoustic properties to meet the design goals, but these coatings set harder than intended when first applied, and will gradually soften to their final state as the parts are flexed and stretched during use. The practical effect of this is that the measured resonant frequency and mechanical damping of a drive unit will shift during the first hours of use, which in turn will alter the drive unit’s acoustic behaviour”.
Get the What Hi-Fi? Newsletter
The latest hi-fi, home cinema and tech news, reviews, buying advice and deals, direct to your inbox.
Matt Dore and the rest of Cambridge Audio’s engineering team explain that, after the run-in-induced relaxation of the suspension, roll surround and spider “reduces the resonance frequency, giving more bass output and allowing the speaker driver to align properly with the enclosure, and any ports or passive radiators”.
During the manufacturing process, materials that make up speaker cones and domes often have internal stresses, too. Comeau gives an example: “Woven fibre or plastic materials are supplied in flat sheet form which is then heat-formed into the required shape and this creates stresses in the material. These mechanical stresses need to be ‘relaxed’ over a period of use.”
This, says Mills, “can cause anything from harshness to a lack of dynamics”. But it isn’t just the drive unit constituents that need to settle: he explains that crossover components such as capacitors, inductors, resistors and cabling also have pre-stressed characteristics that are eased when a signal passes through them. Incidentally, he says this is another reason Fyne Audio cryogenically treats many of its speaker crossovers as this also helps reduce component stresses.
Hours, days or weeks?
So is this an overnight job that can be achieved in the time it takes to defrost a chicken? The frustrating answer is… it depends. (We know, sorry.) At What Hi-Fi? we tend to run all products over two or three full days, and even then it isn’t all that uncommon to hear that some might need longer to settle into the sound we expect. So how many background replays of Chris Rea’s 137-song Blue Guitars album is it going to take?
“We have seen the resonant frequency lower and the response at the top end of the driver's range smooth out after a few weeks,” says Neat Acoustics’ Oakes. “You can hear quite a difference after 30 hours, but some speakers can take over 100 hours to reach their best – it depends on the materials in the drivers and the parameters of the suspension.”
Similarly, PMC’s Thomas says that acoustic behaviour will change during the first 50 hours of playback. And the number of hours Fyne Audio’s Mills suggests is there or thereabouts too: “Whereas considerable improvements can be seen after 40 hours, it can take 10 times that to fully run in. Larger loudspeakers tend to be the worst offenders, as for starters the cones tend to move less.”
Indeed, the speakers that use Fyne’s IsoFlare point source driver array (pictured above) offer one example of why running-in time isn’t a one-fits-all approach. As they have the tweeter unit in the throat of the mid/bass driver, it takes a lot to keep the acoustic centre properly signed. The company says that, like a race engine, tolerances are therefore tight and benefit from a good few hundred hours.
The IAG Group’s Comeau describes the stress-relaxing/time ratio as a curve that is “initially quite steep so that the majority of change is accomplished within a few days, or at most weeks, of use”. He says that while some parts do continue to improve over months, this much more gradual process may not be “readily discernible”.
But according to Comeau, it isn’t just the relaxing of stresses that make running-in important. He argues that as all the numerous parts that make up speakers differ in material, these all need to be running at a stabilised temperature to work harmoniously. “Initially the softer parts will start to warm to room temperature relatively quickly, but heavier parts, especially the drive unit chassis and magnets, will take much longer, up to 36 hours,” he says. “During this time the performance of the drive units will gradually change. You can speed this process up by playing continuous music, which will help dissipate heat to the metal parts, for example, as well as circulating air around inside the speaker enclosure to other components.”
PMC’s Thomas has another tip to hasten the effect: “High-excursion, low-frequency sine waves can speed up this process for bass drivers.”
OK so we’re looking at around 40 hours – roughly four plays of Chris Rea’s Blue Guitars – with more gradual progression perhaps coming down the track too.
However, as with cars nowadays, many products are now burned in for some time by manufacturers before they leave the factory as part of the final stages of testing. This is the case for Cambridge Audio, with Dore stating that such initial sonic changes resulting from the run-in time “are likely to have happened before they reach the customer”.
Considering the discussion so far, it makes sense that speaker manufacturers would run-in every component before using it during the product development stage, too, although it wasn’t something we had really given much thought to before Thomas mentioned it was part of PMC’s process. “It is vital that we only use parts that have fully stabilised their acoustic behaviour, giving us the most accurate representation of each part’s performance,” he says.
What about electronics?
So, case closed: engineers agree that speakers change and benefit from an initial bedding-in period. But what about electronics?
Just as the run-in time depends on the speaker’s materials and driver size and configuration, Chord Electronics’ Matt Bartlett says that “the necessity for a run-in period varies depending on the product type”, with its power amplifiers using Ultima technology apparently benefiting the most from it. (Because of this – and going back to an earlier point – these are already run-in at Chord’s factory before they are shipped.) “In contrast,” he adds, “our preamps are less affected by this process [and] our digital products, such as DACs, streamers, and upscalers, typically do not require running-in.”
Cambridge’s engineers propose that, for components such as amps and streamers, the effects of initial one-off run-ins “can be less clear”, adding: “We’d be concerned about the stability of a design if an amp was sounding significantly different over time.” But more discernible, they say, is the effect a warm-up period before listening can have each time a component is powered on, giving it time to reach its optimum operating temperature. “Temperature definitely has an effect on the measurable and subjective performance of Class A/B amplifiers. A cold amp may have higher intermodulation distortion.” It is why the company – and indeed many others – build thermal compensation into their designs, to allay such repercussions.
Running-in your ears too
It isn’t just the equipment that needs time to adjust but you too. Indeed, another surprise was how many engineers mentioned the effect of psychoacoustics when introducing a new component into your system for the first time. The ears need to run-in too, so to speak. While recognising that it is not theoretically part of the products’ running-in process, IAG’s Comeau says this is “a major factor in evaluating the subjective performance of loudspeakers and should not be overlooked”.
“When changing loudspeakers from one design to another,” Comeau explains, “the ‘filter characteristics’ that the brain has built up when living with the original speakers will have to be erased and replaced by a new filter set which accommodates the acoustic performance of the new speakers in the room. Generally, with well-designed speakers, this happens within a few days or at most a week of use.”
Chord Electronics and Cambridge Audio agree that customers should “allow a period for their ears to adjust to the level of musical information on offer” (Chord’s Bartlett); that you have to “‘get used’ to the sound of new equipment over time, and that becomes your new reference” (Cambridge’s Dore). Meanwhile, Neat Acoustics’ Oakes paints a rather extreme (but feasible!) example: “If someone has been using an old pair of Celestion Ditton 66 for years, listening to a pair of Neat Petites for the first time could be a bit of a culture shock!”
Further to equipment and ears settling, Comeau also proposes that there is an aural adjustment to the room acoustics too. While he says that the human brain has good sound processing abilities that allow it to gauge the room effects on a real instrument such as a piano, he explains that it takes longer with output from a speaker as it is “very different to the point source of an instrument and affects the room acoustics in a different way which, initially, results in some aural confusion. Most of this adjustment/processing is accomplished within a few hours of listening”.
If, he says, the speaker engineer has not considered the off-axis performance, and therefore the reflections from the side walls, floor and ceiling are not similar in sonic character to that of the speaker’s direct sound, then it will take longer for listeners to “accommodate the odd character of the reflections in the room or, at worst, will never be entirely comfortable with the sound”.
MORE:
Nick Clarke interview: Cyrus Audio's MD has an eye to the future
How to set up and position your speakers in 4 simple steps
Pick of the Month: Our verdict on the Sonos Arc Ultra, Copland’s premium valve amp and more
Becky is the managing editor of What Hi-Fi? and, since her recent move to Melbourne, also the editor of the brand's sister magazines Down Under – Australian Hi-Fi and Audio Esoterica. During her 11+ years in the hi-fi industry, she has reviewed all manner of audio gear, from budget amplifiers to high-end speakers, and particularly specialises in headphones and head-fi devices. In her spare time, Becky can often be found running, watching Liverpool FC and horror movies, and hunting for gluten-free cake.
-
Friesiansam For speakers and, headphones too, it makes a lot of sense to run in the moving parts but, cables and solid state electronics, maybe not so. If it really does make a difference to cables and solid state electronics, surely most won't have a transparent enough system to hear that difference or, good enough ears unless young, unlike me...Reply -
Jeremy Psychoacoustics makes sense (we take time to adjust), AB amplification needs a few minutes. The rest makes less sense, especially with the "it depends" comments.Reply
You state that there are measurements demonstrating this effect on speakers... can you publish those please